Reshaping Climate with Geometry: How 3D Printing Enables Clean Tech
by Elissa Ross, PhD. CEO & Cofounder, Metafold 3D
Much has been made of the potential of 3D printing as a cleaner manufacturing methodology. The opportunities for reduced material inputs, goods that are produced closer to the site of consumption, and decreased emissions, not to mention the geo-political motivations for onshoring/reshoring. Indeed all this is true. However, what most people miss about the true promise of 3D printing is that we can make new kinds of things. The force multiplication potential of 3D printing stems from what it unlocks in terms of design rather than improvements in the manufacturing process over existing methods. It is a paradigm shift that requires creativity, knowledge of applications/industries and of course, mathematics.
3D printing throws out the geometric constraints of conventional processes like injection molding, allowing for radically new topologies, which we can roughly think of as the fundamental shape of an object. One way to leverage this freedom to create totally new kinds of parts is to design lattices. Lattices are part of a broader category of metamaterials — repetitive geometries assembled at the small scale (a unit cell) to have target properties at the macro scale. Wood is a naturally occurring example of a metamaterial, where the cellulose structure leads to its well-known anisotropic properties (cutting wood “against the grain” leads to different behaviour than “with the grain”). Building on the idea that macro behaviours can emerge from architecting the cellular properties, engineers have been tinkering with different metamaterials to achieve remarkable behaviours. Examples include lattices with very little material but are nevertheless extremely strong, or lattices with high surface area yet minimal volume. It is only within the last decade that 3D printing has made it possible to fabricate any of these metamaterials.
A direct application of 3D-printed metamaterials to clean tech is process intensification. The goal of process intensification is to make dramatic reductions in the size of unit operations (reactors, heat exchangers, separators etc.) within chemical plants, or to otherwise increase yields in a fixed volume. 3D printing is uniquely positioned to accelerate process intensification because it can manufacture self-supporting lattice structures with a massive amount of surface area.
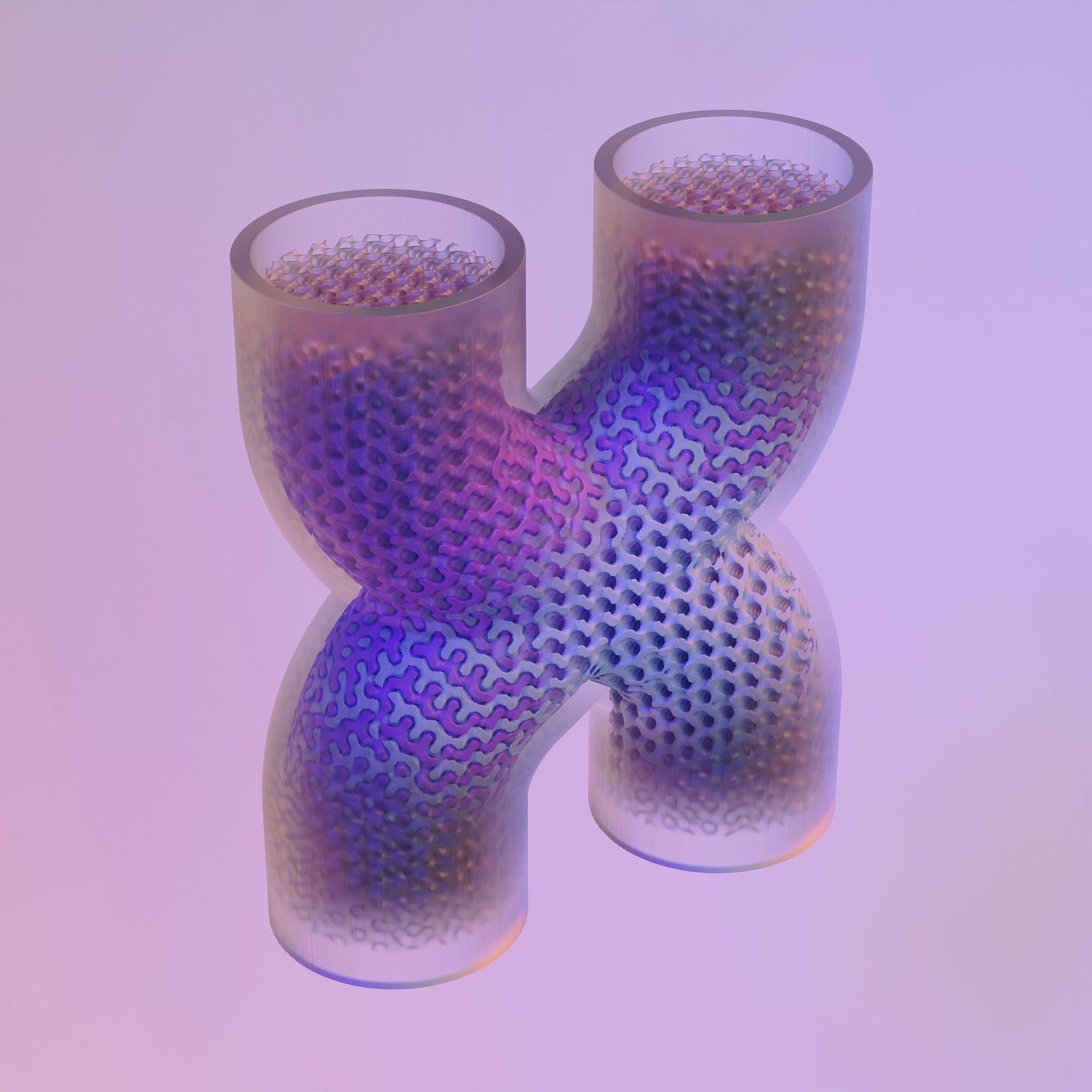
For example, high surface-area 3D printed heat exchangers have demonstrated increased efficiency improvements of 50% or more. While these are currently being used primarily in performance applications, given the ubiquity of heat exchange and the critical role it plays in everyday life, the potential for 3D printing to reimagine energy management is enormous.
Additional examples of process intensification via 3D printing can be found in direct air capture, bioreactors, gasification for syngas and hydrogen, catalysis, and pyrolysis. In all cases, 3D printing and its “unlimited complexity” allow us to pack surface area within smaller volumes, increasing the air-surface interface to capture carbon, transfer heat, filter fluids, incubate stem cells, or otherwise facilitate chemical reactions. Intensifying chemical reactions across a range of industries has the potential to make a huge swath of businesses much more sustainable, but also more competitive.
To achieve these dramatic wins in process intensification, engineers have been turning to special high surface area geometries called Triply Periodic (Minimal) Surfaces (TPMS). These geometries were initially investigated in the 1860s by the German mathematician Hermann Schwarz better known for his work in complex analysis. Notably his work contained no pictures — the existence of TPMS was established through mathematical argument, with no apparent focus on the physical manifestation of these shapes. I’ll skip the rant on the importance of funding pure mathematics, but I conjecture that Schwartz would be shocked to see the broad reach of his research program today.
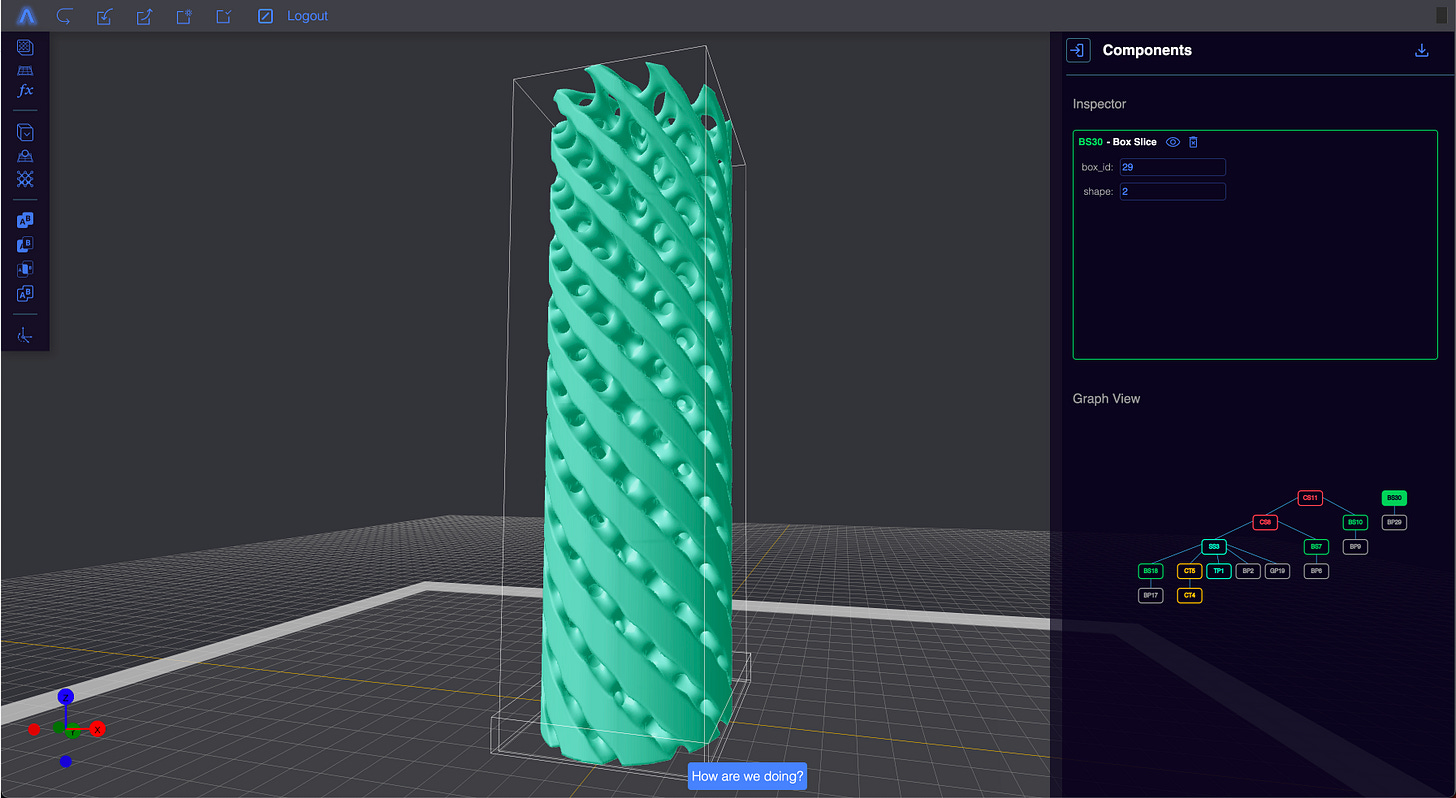
While engineers have embraced the potential of 3D printing and the new shapes like TPMS’s afforded by the methodology, they have also struggled to adjust their geometric mindsets due to antiquated software and companion training. Existing digital design software has led many to spend frustrating hours trying to achieve the promised “free complexity” of 3D printing, waiting for bloated geometry-heavy files to load, process and slice in preparation for printing. Although the developments of the 3D printers themselves have been astonishing over the last decade, the digital pipes that feed the machines have yet to be updated. As a result, many incredible innovations in high surface area clean tech remain on the bench, small-scale prototypes waiting for the digital manufacturing infrastructure to keep up.
While software has lagged behind the flashier improvements in 3D printing hardware, a new class of software application is ready to handle the heightened level of complexity. Up until very recently, the backbone of almost all CAD software was based on licensing one of just a handful of geometry kernels, which dictates and limits the geometry handling of the software. Several startups (mine among them) motivated by 3D printing, have written new geometry kernels that take advantage of GPU acceleration and implicit modeling to actually realize that “free complexity” we were advertised.
More work is required! These same startups face an uphill battle educating and interfacing with engineers and their existing software. The largest challenges are in the pathway from digital model to simulation-ready data, and finally to machine inputs. Currently, the only answer to both questions is to use the “same old pipes” which fundamentally limit the scale and complexity that is possible. Furthermore, the need to reformat data en route to the printer introduces a loss of accuracy that can lead to inconsistencies in the printed parts — repeatability being another massive pain point for the whole industry.

To realize the potential of 3D printing-enabled climate tech, we need cooperation between software and hardware, together with a pressing white hot burning problem (yep, climate change!). Digital Infrastructure that unlocks the true potential of 3D printing can be seen as part of a bigger push for software-enabled climate technology. While money is flowing into the climate sector, it has historically been focused on capital-intensive startups directly attending to the (very important) business of generating cleaner energy. To understand the role of software for 3D printing in climate enablement one needs to be willing to consider the second order effects of these investments. Pushing forward the 3D printing industry is essential in our fight against climate change. But what that looks like right now might be different from the fully-formed final vision.
Certainly, we need innovative engineers working on climate to be educated in 3D printing. We also need forward-looking manufacturers from all industries to prove the potential of 3D printing as a production methodology — adidas broke ground with their 3D printed midsole, followed by all major sportswear brands. Now other industries (including clean tech) are following their brave lead. As capital flows toward the right now problem-solving efforts, let’s also keep our view (and money) on humanity’s longer term projects, too. Like Schwartz’s contributions in pure mathematics, establishing a rigorous foundation now can pay dividends in the future.
✍️ The Draw-down
Pop in and paint with MCJ Artist-in-Residence on February 28! We'll be painting women-founded climate startups to shine a light on their stories in celebration of Women’s History Month. Details and RSVP here.
🍿 The Lean Back
Learn about Epoch BioDesign in the latest Pique Action film.
🎙My Climate Journey Podcast
🌲 Cody talked to Diego Saez-Gil, Founder/CEO of Pachama, and Sam Gill, President/Cofounder of Sylvera about the history of forestry carbon offsets and how they work, some of the challenges highlighted recently, and what they think the path forward looks like.
🔥 Yin spoke to James Sedlak, who leads Operations and Community Engagement at Kodama Systems, about his experience as a wildland firefighter, the mental and physical requirements for the job, the importance of mitigation, the future of firefighting and what the space will entail.
🌊 Oliver Gunasekara, CEO/Cofounder at Impossible Metals, shared his company’s audacious moonshot-like technology to sustainably harvest trillions of dollars of undersea metals and disrupt the EV battery supply chain in the process.
👩💻 Climate Jobs
For more open positions, check out the #j-climatejobs channel in MCJ Slack as well as our job board featuring 76 MCJ portfolio companies and over 500 open positions.
Manufacturing Project & Program Manager at Artyc (Fremont, CA)
Process Engineer at Dispatch Goods (San Francisco or Baltimore)
Director, Carbon Sales at DroneSeed (Remote)
Head of Cell Biology and Cell Line Development Engineer at Hoxton Farms (London)
Data Analyst at Leap (Remote)
Transaction Specialist, Asset Marketplace at LevelTen (Seattle, WA)
VP People and VP Capital Projects at Lilac Solutions, Inc. (Oakland, CA)
Head of Commercialization at Noya (San Francisco, CA)
Senior Manager, Customer Onboarding at Runwise (Remote)
Executive Director at Terraset (Remote)
Staff Equipment/Mechanical Engineer at Twelve (Berkeley, CA)
Senior Accounting Manager at Vesta (Remote)
✨ Highlights
📈 Our friends at The Cool Down released their first public data report analyzing thousands of pieces of climate content they've produced. What they've learned can help inform communicators, politicians, and brands around what really matters most to mainstream Americans on climate topics. Check out the key takeaways from the report here, as well as the full white paper, infographics and more in this folder.
💸 Climate Vault launched a new RFP for emerging carbon dioxide removal (CDR) solutions in the terrestrial, technological, or oceanic pathways. The grant project can fund up to 860,000 metric tons of CDR and seeks to stimulate the growth of innovative technologies that are helping make net negative emissions possible. Details here.
⚡️ Apply for Connecticut's Innovative Energy Solutions Program and receive up to $5M in funding for innovative projects that enable a decarbonized, affordable, and equitable electric grid for CT. Applications are open now! Learn more here.
🗓 February Events
Click the event title for details & RSVP info. For more climate events, check out the #c-events channel in MCJ Slack.
💡 MCJ AMA with David Keith: Best known for his work on the science, technology, and public policy of solar geoengineering, David led the development of Harvard’s Solar Geoengineering Research Program. Post your questions for David in the #c-mcj-ama channel starting TODAY. Details here.
👭 Women in Climate Meetup: Monthly virtual meetup for women who work in, or want to work in, climate. (2/22)
🍻 Minneapolis / St. Paul Meetup: Casual in-person gathering for people interested in the space. (2/23)
👋 Community Welcome Call: Connect, share and learn with the MCJ team and community members. (2/23)
♼ MCJ Monthly Idea Jam, Resource Use + Circularity: These sessions provide a chance for MCJ members to get help with roadblocks, meet co-founders or future employees, connect with investors, or people working on similar topics. (2/24)
🇨🇦 Toronto Climate Tech Social: Everyone is welcome to join the networking, discussion, and kick off this full potential community in Toronto. Feel free to register and bring along +1s/2s/3s! (2/27)
🌎 Overture Insights with Former Deputy National Security Advisor to President Obama Ben Rhodes and Overture co-founders Shomik Dutta and Brandon Hurlbut: Discussing climate change, U.S. foreign policy, and national security. (2/27)
MCJ Climate Voices is a free weekly email curating news, jobs, My Climate Journey podcast episodes, and other noteworthy happenings in the MCJ member community.
💭 If you have feedback or items you’d like to include, feel free to reach out.
🤝 If you’d like to become an MCJ community member, apply today.
💡 Have a climate-related event or content topic that you'd like to see in the MCJ newsletter? Email us at content@mcjcollective.com
"Additional examples of process intensification via 3D printing can be found in direct air capture, bioreactors, gasification for syngas and hydrogen, catalysis, and pyrolysis."
In addition to heat exchangers, all these would seem to have major implications for a variety of advanced energy applications.
Curious how they hold up under the industrial pressures, heat, corrosion, friction, etc. that will be at issue. Good post!
Great article! I’ve been really into the open-source space for 3D printers (firmware and hardware modifications). Also a chemical and environmental engineer by training, so I find these applications really important and exciting. Where do you see the role (if any) for open-source printers and their engineers in moving this forward? For example: using/contributing to software that enables lattice structures? New more efficient file formats? Hardware mods? Also assumed that you’re talking about SLS rather than cheaper tech like FDM.
Would love to chat and learn from you!